
The essence of titanium
A titanium frame combines the best qualities imaginable in a high-quality bicycle. At Luan Bikes, we use Grade 9 alloy (TiAl3V2.5, EN 3.7195), known for its strength, flexibility, and corrosion resistance. Titanium is the preferred choice for demanding riders seeking durability and comfort in their equipment. Here are some of the key benefits of a titanium frame in detail, along with an insight into the manufacturing techniques used by Luan Bikes.
Lightness & Agility
Despite its incredible strength, titanium is extremely lightweight. The spring symbolizes this perfect balance between stability and weight savings – for maximum performance on any terrain.
Titanium also has a natural damping property that absorbs vibrations better than aluminum or carbon. This means that a titanium frame offers a particularly comfortable riding experience, as it absorbs shocks and vibrations better. This property is particularly valuable for long-distance riders and contributes to rider fatigue resistance.
Sustainability & Responsibility
Titanium is not only durable but also fully recyclable. Our commitment to sustainability means we use high-quality, environmentally friendly materials and promote the conscious use of resources. These materials are reusable, as titanium can be melted down and reused without loss of quality, whether for new bicycle frames, aircraft parts, or medical implants.
Indestructible durability
Titanium is rust-proof, corrosion-resistant, and virtually indestructible. The shield represents the durability and protection our bikes offer.
offer – a companion for life.
Whether you're riding through rain, mud, or snow, titanium won't rust! While steel begins to oxidize and aluminum loses its strength under stress, titanium remains unfazed. This makes it a lifelong companion that can withstand even the harshest conditions.
3D titanium frame
The future of bicycle manufacturing
3D printing technology is revolutionizing the production of titanium bicycle frames and opening up completely new possibilities in terms of design, performance and sustainability.
This innovative process enables the production of extremely precise, tailor-made frames and components that conventional manufacturing methods cannot achieve.
A key advantage of 3D technology is its utmost precision and design freedom. While traditional manufacturing processes are limited by material constraints, 3D printing enables complex, organic structures with optimized weight distribution. This creates frames that are both lightweight and exceptionally strong.
Another milestone is the improved stiffness and damping. By applying material to strategic areas of the frame, a perfect balance between ride comfort and direct power transmission can be achieved. This ensures a comfortable ride over long distances while also offering the responsiveness needed for demanding terrain or competition.
In addition to its technical advantages, 3D printing contributes significantly to sustainability. While conventional manufacturing methods waste large quantities of titanium through milling and cutting, the additive process uses only as much material as is actually needed. This not only reduces material consumption but also minimizes the ecological footprint.
A unique feature of 3D technology is the ability to integrate seamless components directly into the frame. This not only creates clean designs with hidden cable routing, but also aerodynamic frames.
About TITAN
.png)
.png)
.png)
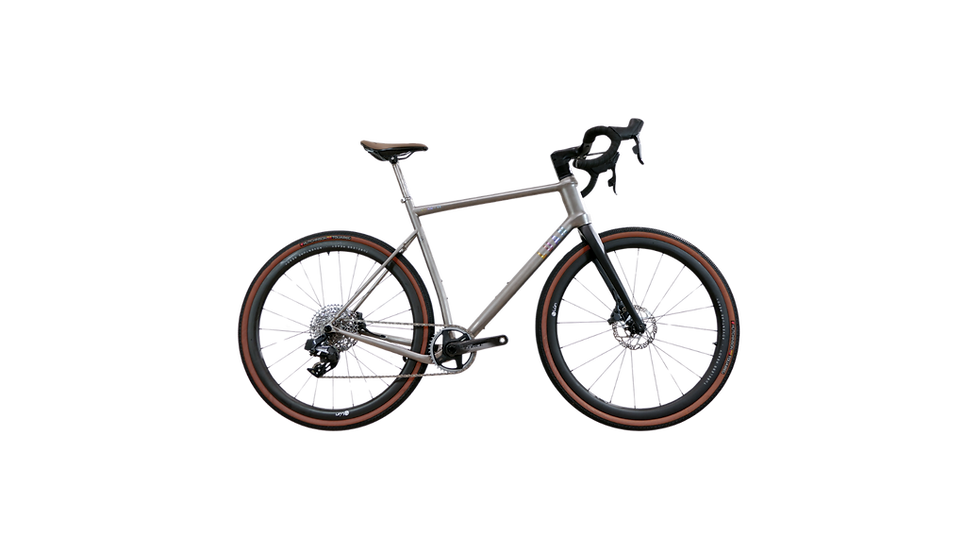.png)
.png)
Good to know
Working conditions
📌 Titanium & Steel (rating: 4/5) have comparatively fair working conditions because production takes place in developed countries.
📌 Aluminum (3/5) is often mined in emerging countries where environmental standards are lower.
📌 Carbon (2/5) is often produced in Asia under poor working conditions (toxins, manual processing).
✏️ Conclusion: Carbon is once again last here – steel & titanium are better.
Good to know
Recyclability (% of material recyclable)
📌 Steel (98%) & titanium (95%) are almost completely recyclable.
📌 Aluminum (90%) is also easily recyclable, but requires a lot of energy.
📌 Carbon (10%) is hardly recyclable – the fibers and resins are difficult to recycle.
✏️ Conclusion: Carbon is the only material that is almost impossible to recycle.
Good to know
Production waste (kg/frame)
📌 Carbon produces the most waste (2.5 kg/frame) because offcuts cannot be recycled.
📌 Aluminum (2.0 kg) also produces a relatively large amount of waste, but is more easily recycled.
📌 Titanium & steel (1.2-1.5 kg) have the least waste, as excess material is often melted down.
✏️ Conclusion: Steel & titanium have the lowest production waste.
Good to know
Water consumption (L/frame)
📌 Carbon (700L) & Aluminum (600L) have the highest water consumption, mainly for material preparation.
📌 Titanium (500L) & steel (450L) need less water because they are usually processed in closed circuits.
✏️ Conclusion: Carbon is again last, titanium & steel perform better.
Good to know
CO₂ emissions (kg CO₂/frame)
📌 Carbon causes the most CO₂ emissions (60 kg CO₂), followed by aluminum (50 kg CO₂).
📌 Steel (40 kg CO₂) & titanium (35 kg CO₂) have lower emissions because they are mostly produced with recycled material.
✏️ Conclusion: Carbon has the worst balance – titanium the best.
Good to know
Material costs (kg raw material/frame)
📌 Titanium & steel require the most raw material because they are very dense metals.
📌 Aluminum & carbon require less material because they can be processed more easily and efficiently.
📌 Carbon has the lowest material consumption because frame production is very material-optimized.
✏️ Conclusion: Carbon seems sustainable here, but the low material consumption is negated by poor recyclability.
Good to know
Energy consumption (kWh/frame)
📌 Carbon has the highest energy consumption (180 kWh) because its production is very energy-intensive (autoclaves, resin curing).
📌 Aluminum (150 kWh) requires a lot of energy for bauxite extraction and electrolysis.
📌 Titanium (120 kWh) & steel (110 kWh) are less energy intensive, but still high.
✏️ Conclusion: Carbon and aluminum are the biggest energy consumers – steel and titanium are more sustainable.

Kriterium | Titan | Aluminium | Stahl | Carbon |
---|---|---|---|---|
End-of-Life-Abfall (kg) | 0.5 | 1.5 | 0.8 | 2.5 |
Wartungsaufwand (Reparaturen/Jahr) | 0.5 | 2 | 1 | 3 |
Maximale Lebensdauer (Jahre) | 50 | 25 | 40 | 15 |
Reparierbarkeit (1-5) | 5 | 3 | 5 | 1 |
Korrosionsbeständigkeit (1-5) | 5 | 4 | 3 | 5 |
Gewicht (kg) | 1.5 | 1.2 | 2 | 1 |
Recycling-Effizienz (%) | 95 | 90 | 98 | 10 |
The following might also interest you about Titan
Titanium is a lightweight, strong, and corrosion-resistant metal widely used in the aerospace, medical, and bicycle industries. It has one of the best strength-to-weight ratios of any metal.
Main properties of titanium:
✔ High strength and low weight – Titanium is about 45% lighter than steel, but similarly strong.
✔ Corrosion resistant – Titanium does not rust and resists salt water, acids and chemicals.
✔ High biocompatibility – Ideal for medical implants as it does not cause any reactions in the body.
✔ Heat resistant – It has a high melting temperature (1,668°C) and is used in aerospace.
✔ Expensive processing – Titanium is difficult to process, which increases production costs.Titanium is mainly mined from ilmenite (FeTiO3) and rutile (TiO2). The leading countries in titanium production are:
Australia (one of the largest suppliers of ilmenite and rutile)
China (largest titanium processor)
Russia
USA
Japan
It is extracted using the Kroll process, in which titanium oxide is reduced with magnesium to obtain pure titanium.
Titanium is used in many high-tech areas due to its special properties:
✅ Aerospace – aircraft parts, engines, space components
✅ Medical technology – implants, prostheses, surgical instruments
✅ Bicycle industry – High-quality titanium frames for road bikes & mountain bikes
✅ Automotive industry – high-performance components, especially in sports cars
✅ Shipbuilding – Titanium alloys for submarines & offshore facilities
✅ Watches & Jewelry – Scratch-resistant luxury watches & jewelryTitanium can also be processed using 3D printing, which is particularly important for complex geometries and customized parts.
Titanium 3D printing processes:
Selective laser melting (SLM) – Titanium powder is melted with a laser.
Electron beam melting (EBM) – Titanium powder is melted using an electron beam.
Direct metal laser sintering (DMLS) – A powder bed is selectively sintered.
Advantages of titanium 3D printing:
✔ Reduced material waste – Only as much material is used as needed.
✔ Complex designs possible – components with internal channels or lightweight structures.
✔ Lighter weight – Perfect for aviation & medical technology.
✔ Fast prototyping – Designs can be tested faster.🔹 High costs – Titanium is more expensive than aluminum and steel, both in terms of raw material procurement and processing.
🔹 Difficult machining – Titanium wears out tools faster and requires special machinery.
🔹 Flammability in powder form – Titanium powder is highly flammable, which makes handling difficult.🌍 Sustainability: Recycling of titanium is improved to reduce environmental impact.
🚀 New alloys: Research projects are developing titanium alloys that are even lighter and more resistant.
🏭 Increased use of 3D printing: Companies are increasingly using 3D printing for customized titanium products.Titanium is a high-quality, high-tech material that impresses with its strength, lightness, and corrosion resistance. It plays a key role, especially in the aerospace, medical, and bicycle industries. 3D printing makes it possible to process titanium more efficiently and with less material waste. Despite its high cost, it remains one of the best metal options for demanding applications.